Dye (p. 106 )
1. Produced in Kyoto City, Kyoto-Fu.
2. Characteristics: Gorgeous and picturesque designs, dyed in multicolors also called "Hon(main)Yuzen." One of the design dyeing using glue resistant. "Tegaki" means hand-painted. Most famous dyeing applied on Kimono. "Itome"(thread line) is the white outline left in the designs after the dying process is completed.
3. Uses: Cloths for "Furisode" (gorgeous Kimono with long hanging sleeves), "Tomesode"(formal Kimono) and "Homongi"(visiting Kimono), all for women.
4. History: The bleaching of hemp and plant dyeing existed since the old days in the Kyoto area. But the rapid development in dyeing techniques occurred in the Nara Period when exchanges started with China and Korea. The origin of "Yuzen Dye" is said to be "Kokechi"(batik), one of the Three Press Dyes in Tenpyo. The batik was originated in India and transmitted to Japan via China. In the Nara Period, melted wax was applied on cloth as a resistant and was removed after the dyeing process. "Rokechi" was not produced in the Heian Period but was revived around the end of the Muromachi Period when "Wa Sarasa,"(Japanese printed cotton) was produced and designs by wax resistant method was revived. During the Kanei Era in the Edo Period,"Chaya Zome" was produced. Designs of natural features in the 4 seasons were dyed with the use of "Yoji Nori"(tooth pick glue), made of sticky rice, and "Tsutsu Nori"(cylinder glue), with a cylinder and pushed out of its tapering end. "Yuzen Zome" is a dyeing process for multi-colored designs invented in 1688-1704 ,by Yuzensai Miyazaki,painter of designs for folding fans in Kyoto. The "Yuzen Zome" process uses the "Rokechi" technique from Nara, "Sarasa Zome" and "Tsujigahana" techniques from the Muromachi Period and the "Chaya Zome" technique from the Edo Period. The "Yuzen Zome" dyeing was applied to cotton and has become much popular.
Dyeing Method
1.Sketching the design.
2. "Jinoshi" - straightening of the cloth.
3. "Sumi Uchi" - marking with Chinese ink the area for cutting with scissors and the area for folding the sleeves.
4. "Kari Eba" - Temporary tailoring.
5. "Shita E" - Sketching the design with "Aobana," juice from the flower of "Murasaki Tsuyukusa"(dayflower.)
6. "Shinshi Hari" - Stretching the cloth with tenter hooks as temporary tailoring.
7. "Itome Nori" -Applying glue resistant to the outline of the design with a cylinder.
8. "Ji Ire" - "Gojiru," juice of ground soybeans, is applied all over the cloth.
9. "Sashi Yuzen" - Dyes are put on the design with a brush and a brush pen.
10. "Mushi" -Steaming the cloth in high temperature in a steaming box to fix the dye.
11. "Fuse Nori" - Glue is applied on the dyed design to make it resistant to the dye on the background.
12. " Ji zome" - The back ground is dyed with a big brush and the cloth steamed again.
13. " Mizu Arai" - Washing the cloth so that all resistant is removed.
14. "Yunoshi" - Steaming to remove wrinkles from the cloth and straightening and fixing the width of the cloth.
15. "Inkin" and "Shishu" - Decorating the cloth with gold leaf and/or embroidery.
16. "Age Eba" - Temporary tailoring and finishing with special care the design to be fixed well.
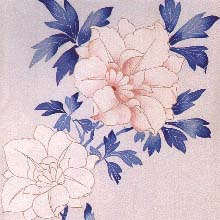
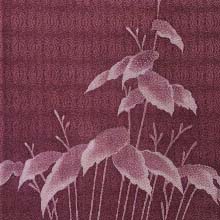
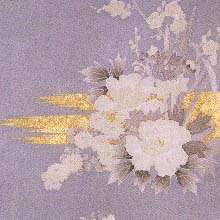
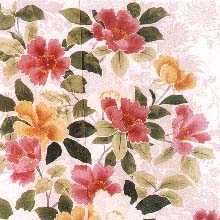